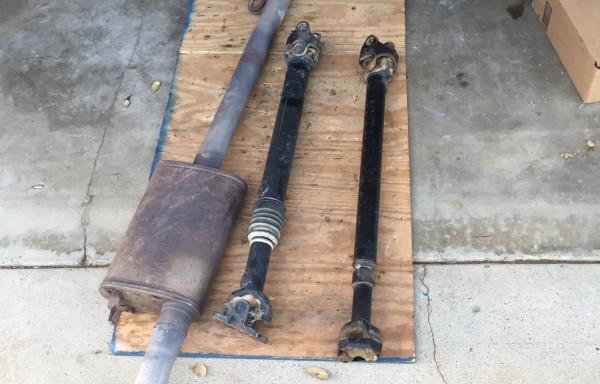
Welcome to part 16 of our 5.2 magnum swap, follow along as we swap a 5.2 magnum from a 1993 ZJ into our 2004 4.0 WJ. No one expects 5 days of over 90 degree weather in the middle of October, but there are just something we cannot plan for.
Read The Rest
Part 1: It’s Finally Happening
Part 2: Out With the Old
Part 3: The Last of the Stock Components
Part 4: All About Brakes
Part 5: Pulling the 5.2 (time lapse)
Part 6: The Test Fit
Part 7: Cutting and (not) Fitting
Part 8: Broken and Upgraded Parts
Part 9: Leaky Plenum Gasket
Part 10: Side Projects and Summer Fun
Part 11: Setting the Motor
Part 12: Custom Exhaust & Driveline
Part 13: Cutting and Rebuilding
Part 14: Giant Radiator in a Little Jeep
Part 15: Custom Tube Bumper
Part 16: Driveshafts
Part 17: A Real Firewall
Part 18: Starting Final Assembly
Part 19: Extending The Engine Cage
Part 20: Still Assembling
Part 21: It Lives!
Part 22: Brakes and Wiring
Driveshafts
This week was slow in the shop. After a week of cool weather and rain we were excited for Fall and looking forward to some reasonable shop temperatures. But our excitement was short lived as summer made a comeback. Due to the weather and a member of the shop crew using his entire weekend to move, it was a slow week at Three Thirds Fab.
We spent some time online looking into loose ends including our fuel, transmission, power steering, and remote oil lines, Mopar performances PCMs, alternator writing, and posting the parts we are not reusing on eBay. In the shop, we spent some more time on the frame plates and took at our driveshafts.
After we finished our half case swap we were able to bolt up the transfer case and take a final measurement for the driveshafts. The hope was that we would be able to reuse our current shafts as we have already had them custom made to our old driveline. With the motor being a little shorter, the transmission being a little longer, and a slightly different transfer case we knew it would be a long shot.
After bolting up everything it looks like the transfer case is only pushed back about an inch, which is very lucky considering the front of the engine is back almost 5”.
The Front
Because the front differential sits on the driver side i-beam, it doesn’t have as much vertical movement as a differential on a straight axle. We are hoping this plays in our favor or we will need to lengthen it by an inch. Our main concern is how much the splines contact while fully drooped.
The Rear
With the rear driveshaft measurement being about an inch shorter we are concerned that it will bind up at full compression. After looking at our current shaft it looks like our limiting factor may be the dust boot. The dust boot may be compressing and binding long before the shaft does. We are going to cut it off and test fit at full compression. If the old driveshaft will work we will make a new neoprene dust boot that won’t bind as much as the rubber accordion style.
What’s Next
With the weather dropping into to mid 80s (10-15 degrees cooler) we are hoping to finish the firewall and mount the radiator and fans.
Don’t forget to check back next Tuesday for updates.
Read The Rest
Part 1: It’s Finally Happening
Part 2: Out With the Old
Part 3: The Last of the Stock Components
Part 4: All About Brakes
Part 5: Pulling the 5.2 (time lapse)
Part 6: The Test Fit
Part 7: Cutting and (not) Fitting
Part 8: Broken and Upgraded Parts
Part 9: Leaky Plenum Gasket
Part 10: Side Projects and Summer Fun
Part 11: Setting the Motor
Part 12: Custom Exhaust & Driveline
Part 13: Cutting and Rebuilding
Part 14: Giant Radiator in a Little Jeep
Part 15: Custom Tube Bumper
Part 16: Driveshafts
Part 17: A Real Firewall
Part 18: Starting Final Assembly
Part 19: Extending The Engine Cage
Part 20: Still Assembling
Part 21: It Lives!
Part 22: Brakes and Wiring
Follow us at www.facebook.com/ThreeThirdsFabrication for updates and more stories.